Shell moulding die
shell moulding dies in vadodara,shell moulding dies in vadodara,shell moulding dies in vadodara,shell moulding dies in vadodara
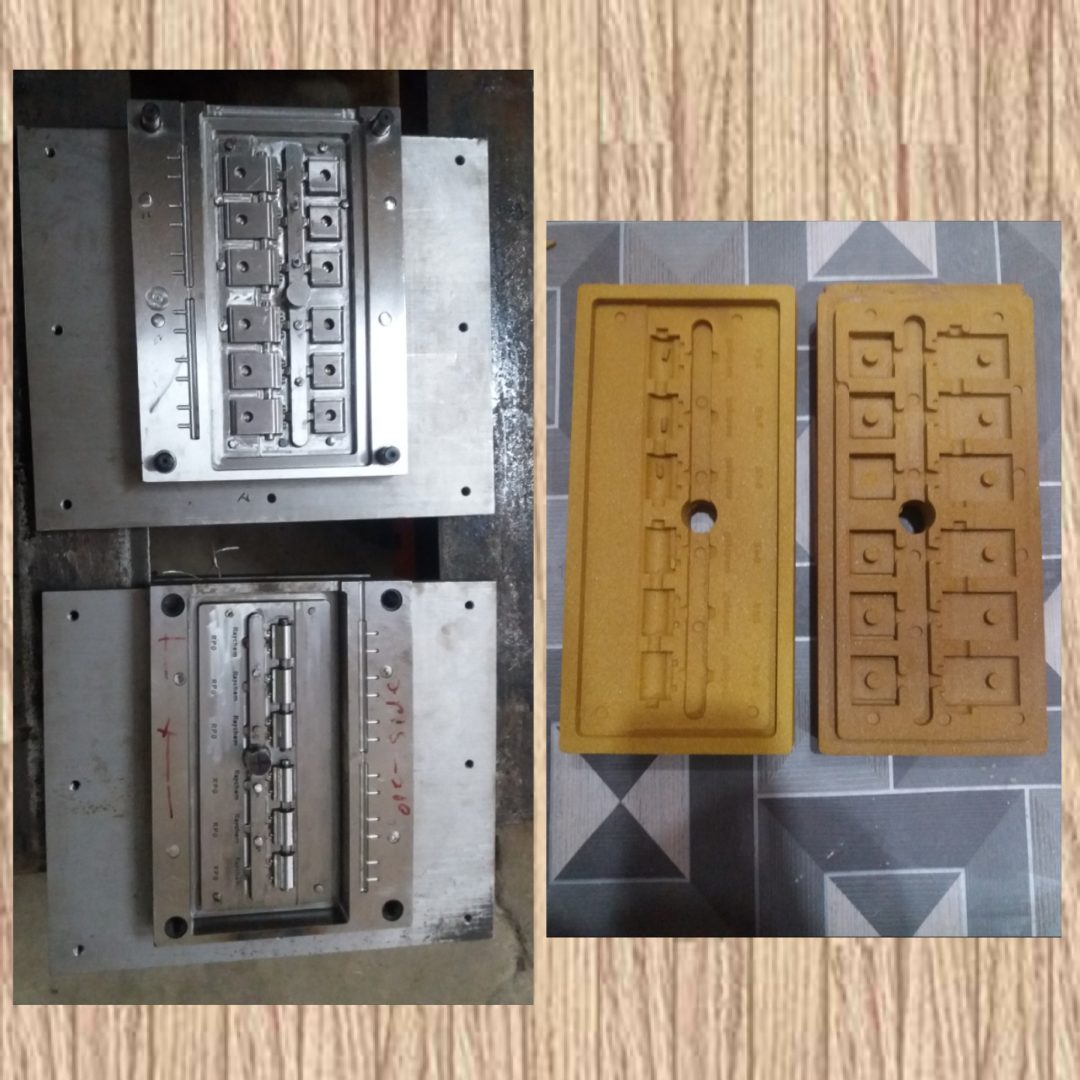
shell moulding dies is still the most prevalent form of casting. It is a conventional molding and metal casting process as the mold may be poured without shell moulding dies in vadodara. The mold is formed around a pattern by ramming sand, mixed with the proper bonding agent, onto the metal or wood pattern. Then the pattern is removed, leaving a cavity in the shape of the casting to be made soshell moulding dies so shell moulding dies in vadodara.
Sand cores are placed if internal cavities or undercuts are required. Molten metal is poured into the shell moulding dies in vadodara, and after it has solidified the mold is broken and castings are removed for secondary process and final finishing.
The shell moulding dies after the skin gets removed from the pattern. The two halved of the shell mold are secured shell moulding dies in vadodara and the metals id poured in the shell to form the part. Once the metals solidified, the shell is broken.
These offered products are manufactured using supreme grade quality components that is sourced from reliable vendors of the market keeping in mind set industry norms. Tested on various quality parameters, to deliver the quality approved range for our respected customers at nominal market price so shell moulding dies in vadodara.
shell moulding dies a process for producing simple or complex near net shape castings, maintaining tight tolerances and a high degree of dimensional stability. Shell moulding is a method for making high quality castings. shell moulding dies in vadodara of precision can be obtained in a wider range of alloys and with greater flexibility in design than die-casting and at a lower cost than investment casting.
shell moulding dies in vadodara that the foundry had not standardized its production processes in different areas. In this review several casting defects and their occurrence cause were identified. This will help in analysing the defect and remedies to overcome them. Casting Rejection on the basis of the casting defects should be as minimum as possible for improved quality. One can continuously control rejections by taking in to consideration different parameters at every stage of production. Therefore it is essential for a metal caster to have knowledge on the identification of type of defect and be able to identify the exact root cause, and their remedies. Hence this systematic work will be fruitful for quality casting manufacturing.
shell moulding dies diagrams were developed by Kauro Ishikawa of shell moulding dies in vadodara thus are often called Ishikawa Diagrams. They are also known as fishbone diagrams because of their appearance (in the plotted form). Cause and effect diagrams are used to list systematically the different causes that can be attributed to a problem (Effect-Y). By carrying out systematic analysis of casting rejection using Parato charts 82-20 principle a definite cause of defect can be known. A cause-and-effect diagram can aid in identifying the reasons why a process goes out of control and once its cause is identified then it can be overcome by various remedies.
Contact Info
+91-9725421076
+91-9714288779
info@unisoncorporation.in
About Company
We are a team of professional who were working with industries of repute in the fields like Precision Component Manufacturing, Injection Molding dies, machine tools , jig & fixture development.