orthopedic part die casting
orthopedic part die casting
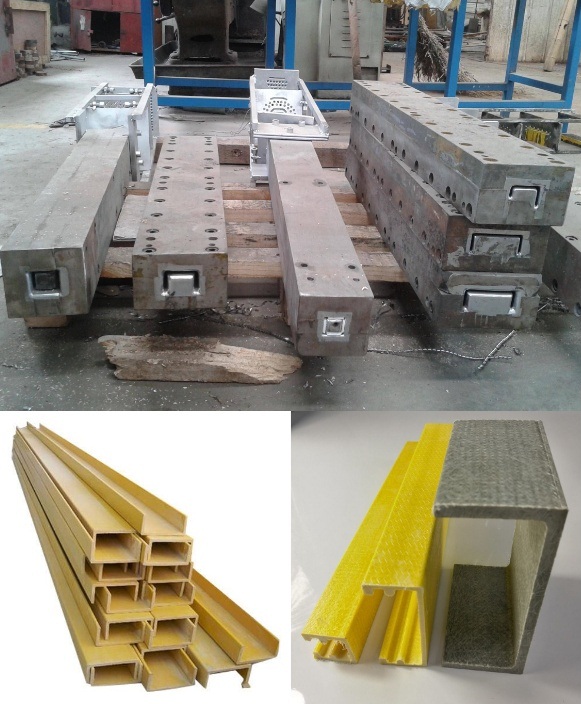
orthopedic part die casting
Unison Corporation are expert in orthopedic part die casting, vacuum forming die, turbine blades, machinery parts, orthopedic surgical part manufacturer.
several such patterns are assembled here you can see here. So, this is the central tree now around which say they used to make a ceramic slurry. So, the ceramic slurry this is kept inside a flask now, the ceramic slurry they used to pour inside. So that the ceramic slurry would fill the entire flask and the ceramic slurry would go around each and every pattern and it used to take the shape of the extreme fine details then, in such a state the ceramic slurry would be dried out of this ceramic slurry is dried out then they used to heat this system then what will happen? The would melt and it used to drain out then they will pour the molten metal into the mould.
All equipment is effected to breakdown, and the function to replace or repair the defective unit so the production can be restored, is called maintenance. Maintenance is one of the important branches in the modern production thinking. The reasons are the increasing of complexity of the modern machines and equipment, investment return time, cost of maintenance, and orthopedic part die casting.
orthopedic part die casting in vadodara baroda gujarat makarpura
Unison Corporation have quality of orthopedic part die casting in vadodara baroda gujarat makarpura. Degasification mainly eliminates the unwanted gases from the mould by bubbling at the bottom of the container as shown in the above figure and it controls the porosity to a much larger extent. Porosity control in aluminum castings can be done in following ways .Hydrogen content in the molten metal decreases by increasing the degassing time. Degassing should be done at optimum temperature. The degassing should be done at lowest temperature because as the temperature increases, the volume of the gas that passes for degassing increases.
Die coat in the gravity die casting in order to obtain smooth surface finish and to avoid direct exposure of mould to the molten metal in order to avoid direct sand casting manufacturers. The material used for die coating is generally calcium carbide and silicon mixture and graphite. The overall motive of this paper is to make an analysis so that a relation between casting defects can be sand casting manufacturers. The study depicts that in practical circumstances it is not necessary to apply special techniques to minimize the casting defects such as computer simulation etclost foam mold casting.
orthopedic part die casting the number and/or size of feeders and gating elements are much higher than their respective optimal values, In this paper an effort has been incorporated to study the change in process parameters and their consequent effects on casting defects. gravity die casting mould in baroda the heat capacity of molten alloy rises with increasing temperature of the pouring, what results in the increase of filling time.
The importance of assessing the compressibility of fiber reinforcements becomes apparent when one is concerned with a part design composed of layers of different reinforcement materials. In order to define a stack structure and/or a processing window,lost foam mold casting of the fiber reinforcements must be known lost foam mold casting in vadodara. orthopedic part die casting for the pultrusion process, one needs to estimate the number of rovings which are needed to fill a given cross section, according to the compaction pressure and the number and type of planar reinforcements defined for the profile.
Contact Info
+91-9725421076
+91-9714288779
info@unisoncorporation.in
About Company
We are a team of professional who were working with industries of repute in the fields like Precision Component Manufacturing, Injection Molding dies, machine tools , jig & fixture development.